Principle of Operation
Relatively high voltage, high current electricity is passed between two electrodes, spaced apart, creating an electrical arc. Inert gas under pressure is passed through the arc into a sealed container of waste material, reaching temperatures as high as 25,000 F (13,900 C) in the arc column. The temperature a few feet from the torch can be as high as 5,0008,000 F (2,7604,427 C). At these temperatures, most types of waste are broken into basic elemental components in a gaseous form, and complex molecules are separated into individual atoms.
The reactor operates at a slightly negative pressure, meaning that the feed system is complemented by a gaseous removal system, and later a solid removal system. Depending on the input waste (plastics tend to be high in hydrogen and carbon), gas from the plasma containment can be removed as syngas, and may be refined into various fuels at a later stage.
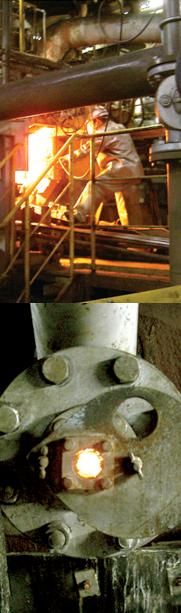
The latest independent review of plasma technology providers was undertaken by Juniper Consulting in 2008, as well as a separate independent review on Alter NRG /Westinghouse technology.
Existing facilities
National Cheng Kung University - Tainan City, Taiwan (PEAT International)
PEAT International constructed a plasma arc waste disposal facility at National Cheng Kung University (NCKU) in Tainan City, Taiwan, which uses its proprietary Plasma Thermal Destruction Recovery method. The facility is able to handle 35 metric tons (3.35.5 short tons) of waste per day from a variety of waste streams, including incinerator fly ash, medical waste, organic industrial process waste and inorganic sludges. It can also process waste consumer batteries and other materials, including heavy metal sludges, and refinery catalysts (waste streams that would generate valuable metal alloys). The facility was constructed as part of a comprehensive resource recovery facility funded by the Taiwanese government, marking the first time the Government of Taiwan committed financial and technical resources to the utilization of plasma technology. It was commissioned in November 2004 and received its operating permit in January, 2005. PEAT has been an active participant in the operations and maintenance of the facility on behalf of NCKU for its research purposes.
The latest independent review of plasma technology providers was undertaken by Juniper Consulting in 2008, as well as a separate independent review on Alter NRG /Westinghouse technology.
Existing facilities
National Cheng Kung University - Tainan City, Taiwan (PEAT International)
PEAT International constructed a plasma arc waste disposal facility at National Cheng Kung University (NCKU) in Tainan City, Taiwan, which uses its proprietary Plasma Thermal Destruction Recovery method. The facility is able to handle 35 metric tons (3.35.5 short tons) of waste per day from a variety of waste streams, including incinerator fly ash, medical waste, organic industrial process waste and inorganic sludges. It can also process waste consumer batteries and other materials, including heavy metal sludges, and refinery catalysts (waste streams that would generate valuable metal alloys). The facility was constructed as part of a comprehensive resource recovery facility funded by the Taiwanese government, marking the first time the Government of Taiwan committed financial and technical resources to the utilization of plasma technology. It was commissioned in November 2004 and received its operating permit in January, 2005. PEAT has been an active participant in the operations and maintenance of the facility on behalf of NCKU for its research purposes.
Yoshii, Utashinai, and Mihama-Mikata, Japan (Hitachi Metals Ltd.)
Three similar small plants are in operation in Japan a 166-short-ton (151,000 kg) per day "pilot" plant in Yoshii, co-developed by Hitachi Metals Ltd. and Westinghouse Plasma, which was certified after a demonstration period in 19992000; a 165-short-ton (150,000 kg) per day plant in Utashinai City, completed in 2002; and a 28-short-ton (25,000 kg) per day plant commissioned by the twin cities of Mihama and Mikata in 2002. Two similar facilities run by different companies in Australia and Germany closed after changes in senior management.
Ottawa, Ontario, Canada (Plasco Energy Group Inc.)
A new and different type of plasma arc waste conversion that uses plasma to refine gases produced during waste conversion, rather than to destroy waste by brute force as do other plasma systems, has yet to show itself to be successful on a full commercial scale. Plasco Energy Group completed a plasma-arc waste demonstration plant in Ottawa, Canada at the Trail Road Landfill, to process 85 metric tons (94 short tons) per day of municipal solid waste. Unlike other plasma waste processing facilities, Plasco Energy Group's process does not use plasma to destroy waste, but rather to refine gases produced during waste conversion, in order to allow them to be used to run an internal combustion gas engine. On 24 October 2007, the Plasco Trail Road facility began delivering power to the grid.
The Plasco conversion system, which uses plasma to refine gases rather than expose them to extremely high temperatures, and whose liner is composed of refractory brick rather than metal, is not susceptible to premature attack of vessel liners. Plasco's internal studies claim that its emissions are also much lower than any other thermal waste processing system. By converting waste to CO2 and water, rather than to methane, the greenhouse gas emissions of the process might be much less than competing technologies such as landfills. Plasco Energy is proposing a scaled up residual waste plasma gasification facility for Los Angeles, California.
In an update to local area residents on 6 December 2008, Plasco president Rod Bryden said delays at its facility were caused by malfunctioning machinery, not problems with the waste-to-energy technology.
The Plasco conversion system, which uses plasma to refine gases rather than expose them to extremely high temperatures, and whose liner is composed of refractory brick rather than metal, is not susceptible to premature attack of vessel liners. Plasco's internal studies claim that its emissions are also much lower than any other thermal waste processing system. By converting waste to CO2 and water, rather than to methane, the greenhouse gas emissions of the process might be much less than competing technologies such as landfills. Plasco Energy is proposing a scaled up residual waste plasma gasification facility for Los Angeles, California.
In an update to local area residents on 6 December 2008, Plasco president Rod Bryden said delays at its facility were caused by malfunctioning machinery, not problems with the waste-to-energy technology.
Slag generated in the plasma-arc centrifugal treatment process meets all applicable Environmental Protection Agency disposal requirements |
Faringdon, Oxfordshire, England (Advanced Plasma Power)
Advanced Plasma Power has built a Gasplasma modular test facility in Faringdon, Oxfordshire that uses refuse-derived fuel feedstock to produce hydrogen, syngas, energy and vitrified gravel. APP have also commissioned a commercial test facility in Swindon, Wiltshire and have plans for a larger 100,000-tonnes/yr-sized commercial or municipal gasplasma facility in the UK.
Swindon, Wiltshire APP
The heart of this technology, the Gasplasma process, forms the basis of APP Swindon Plant, the first Gasplasma facility in the world. Gasplasma is the sequential use of gasification, plasma gas treatment, syngas polishing and gas engine power generation.
A full scale plant will treat 100,000 short tons (91,000 t) per annum of municipal waste and produce:
Enough power for 10,000 homes
Enough heat for around 700 homes
over 99% landfill diversion of feedstock with minimal residues and emissions
Increase recycling rates by over 20%
High performance, high-value aggregate glass (trademark Plasmarok)
Novel combination of three existing and proven technologies (termed Gasplasma)
Negative carbon footprint and lowest environmental impact plant and building
A full scale plant will be 150 metres (490 ft) long, 50 metres (160 ft) wide, and along most of its length only 11 metres (36 ft) high. Above the thermal plant, the roof height is about 14 metres (46 ft), and the single exhaust for the engines 10 metres (33 ft) higher, at only 34 metres (110 ft). The building is approximately the size of a supermarket store and operates under a light vacuum, meaning it contains all odors. The entire process occurs within the building.
Planned facilities
St. Lucie County, Florida (GeoPlasma)
The first plasma-based waste disposal system in the USA was announced in 2006 in St. Lucie County, Florida. The county stated that it hopes to not only avoid further landfill, but completely empty its existing landfill 4,300,000 short tons (3,900,000 t) of waste collected since 1978 within 18 years. The plant was scheduled to come into operation in 2009. However, no permits as yet have been submitted for construction. Backers have announced that the facility would produce 600 short tons (540,000 kg) of solid rubble from around 3,000 short tons (2,700,000 kg) of waste per day at 5,500 C (9,900 F). Uncertainties have arisen however regarding the safety of such a facility. The public and environmental threats from incinerators coupled with the uncertainty of the community's ability to produce such large quantities of waste consistently have led GeoPlasma to submit a new proposal for a much smaller facility that would convert 200 short tons (180 t) of waste per day.
Vancouver, British Columbia, Canada (Plasco Energy Group Inc.)
A proposed Plasma arc gasifier has been planned for the Metro Vancouver area. However residents of the area have protested. Metro Vancouver is currently conducting an RFP process to determine a long-term solution for waste management. Plasco is not proposing that Metro Vancouver discontinue the RFP process, but rather to establish an interim solution that can quickly address the shortfall in landfill capacity, while also providing a facility that will allow Metro Vancouver to closely scrutinize and evaluate this new technology as part of its long-term decision making process.
Port Hope, Ontario, Canada (Sunbay Energy Corporation)
Utilizing technology licensed from Europlasma, the plasma arc facility proposed for lands in the vicinity of Wesleyville in Port Hope, Ontario (approximately 45 minutes east of Toronto) will handle 400 short tons (360 t) per day of Municipal Solid Waste (MSW) and Tire Derived Fuel (TDF). Sunbay Energy is currently obtaining the required approvals from Provincial authorities and intends to have the facility operational during the 4th Quarter of 2009.
Tallahassee, Florida (Green Power Systems)
The city of Tallahassee, Florida has signed the largest plasma arc waste to energy contract (35 MW) to date with Green Power Systems to process 1,000 short tons (910 t) daily from the city and several surrounding counties. Completion of the project is scheduled for October 2010.
Hirwaun, Wales (EnviroParks Limited)
EnviroParks Limited plan (31/9/07) a consortium to build an Organic Park in Tower Colliery at Hirwaun, South Wales. This includes a plasma gasification plant combined with advanced anaerobic digestion to divert municipal solid waste from the landfill. Enviroparks are currently collaborating with partner Europlasma of Bordeaux to provide the plasma gasification unit to the park.
As much as 60 million is being put into the project by EnviroParks Ltd and its partners, to establish organic waste and mixed waste treatment facilities next to the Tower Colliery at Hirwaun. The Hirwaun site itself is large enough for the processing of over 250,000 metric tons (280,000 short tons) of non-hazardous waste a year. Initially, though, an anaerobic digestion plant will be designed to handle 50,000 metric tons (55,000 short tons) of organic wastes a year.
Jackson, Georgia (PR Power Company)
PR Power Co. plans to open a plant south of Atlanta, near Jackson, Georgia, that will use a "plasma torch" to vaporize tires down to their natural elements mainly hydrocarbons and scrap steel. The gases will be converted to electricity for sale to electric utilities and the scrap steel will be sold at an estimated $50 a ton.
Red Deer, Alberta (Plasco Energy Group Inc.)
Plasco is preparing to start construction on a commercial-scale facility in Red Deer, Alberta in the Summer of 2009. This facility, the company's first commercial plant, is expected to be completed by the end of 2010.
Maharastra Enviro Power Limited, SMSIL Pune, Maharastra India
SMS Infrastructures Limited (SMSIL), Central India largest civil engineering and infrastructure development company, constructed 68 tonne-per-day hazardous waste-to-energy plants, located in Pune, India, that will use Westinghouse Plasma Corporation (WPC) plasma technology and reactor vessel design. Each plant will provide comprehensive disposal services for a wide variety of hazardous waste, and will produce up to 1.6 MW (net) of electricity
The facilities will be the largest plasma gasification WTE plants in the world processing hazardous waste.
Concerns
Numerous municipal plasma arc gas plants (see above) are currently in development, including one for the city of Los Angeles. Practical (limited use of land space for landfills), technological (large-scale use of technology versus small-scale, e.g. plasma arc is currently favored as a means to destroy medical and hazardous waste), logistical (transportation infrastructure requirements) and budgetary considerations can affect the viability of individual projects. It is important to note that no municipal-scale waste disposal plasma arc facilities have as yet been constructed, which could present a considerable technological and budgetary challenge to even the largest municipalities.
An issue regarding plasma systems that rely on high temperatures for processing is in the life of their liners. The liner is an important aspect of separating the high interior temperatures of the plasma system from the [metal] shell of the plasma container. Liners are highly susceptible to both chlorine attack and to local variabilities in [high] temperatures, both of which would be found with typical municipal waste systems, and are not likely to last more than a year in service. This concern can be addressed by using the method demonstrated at the Trail Road Plant in Ottawa, Canada, which requires lower temperatures and a more robust material (brick) for a liner instead of the expensive and fragile metal. (ArticlesBase SC #2313832)
For every natural resource that is being use to produce something will eventually end up as waste.
ReplyDeleteInSinkErator Evolution Compact